BoltTight
Bolted joints tightness and pre-tension monitoring with smart washers
Introduction:
Operational environmental factors including vibration, severe loading, temperature cycling, fatigue, external forces (wind, thermal expansion, earthquakes), erosion, and corrosion are typical causes of the bolted joints failure in structures, piping, machinery, wind turbines, and applications using bolted joining.
Thanks to the advancement in low paower micro-scale electronics and connectivity and our proprietary technology of precision clamping force measurement, S5 System has developed a completely non-invasive, wireless intelligent real-time monitoring of tightness and tension of critical bolted joints using Smart washers with minimal extra footprint. BoltTight washers precisely measure and send the compression and clamping forces in a bolted joint to the monitoring system for real-time and historical data logging, preventive and condition-based maintenance, and reliability analysis to ensure the integrity of the joints is not compromised.
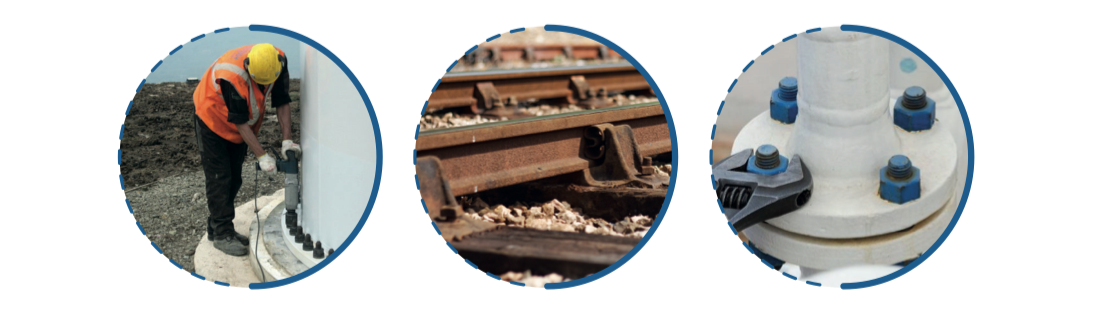
The Problem:
The biggest challenge in bolted connections is to ensure that the bolted joint has achieved or retained the required bolt load. Historically, bolts break or loosen due to fatigue issues, metallurgic phenomena, maintenance re-torquing, torque testing, or micro-movements. Incorrect tool settings or bolt load during assembly can cause critical problems during the operation phase. The cost impact of periodic check-ups and re-tightening procedures is very high. Critical equipment like cranes and wind turbines undergo lengthy and laborious bolted joint maintenance procedures. The usual practices like torque testing are ineffective when the joints and fasteners are not new; the bolts make microscopic welding to the adjacent material and represent high torquing resistance which falsely indicates that the joint is tight while there is no accurate indication of the compression and joining the clamping force.
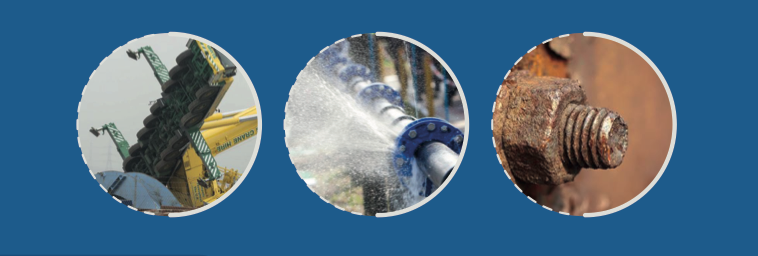
The Solution:
To address these problems, S5 System has invented BoltTight washers, a purpose made to prevent the less effective check-ups and ensure that the compression of the bolted joints is safely and securely monitored for the duration of the asset lifecycle.
BoltTight uses proprietary technology to monitor the compression force in bolted joints constantly. These washers are designed in major standard metric and imperial sizes with different materials. The design and manufacturing aimed the product to be highly robust, non-invasive, with real-time wireless monitoring. Our innovative solution is real-time maintenance-free, hermetically sealed sensors completely embedded inside the washers without compromising their integrity, with protection from extreme temperatures, pressure, shock, water, dirt ingress, and vibrations and designed to suit a wide range of GET including teeth and adapters.
Installation of these washers is the same as any standard washer. No extra special tools are required. No calibration is needed, and the temperature and other environmental factors cannot compromise the accuracy of the data.
Washers send data using ZigBee wireless technology to a hub that collects data from all the nearby washers and transfers it to the server for analytic and monitoring, and data storage purposes.
Any critical failure can be detected, and a real-time audio-visual alarm notifies the operation and maintenance team of the joint by indicating the exact location of the failed bolt in the plant 3D models for quick tracing of the problem and response.
Thanks to the lower cost of ownership, the return on investment can usually be realised in a few months.
Currently, in the market, there are few bolted connection intelligent solutions. Some use ultrasonic or other non-destructive test tools, which are expensive and require manually checking every single joint by experienced technicians. There are smart bolt options attempted in the market; however, embedding electronics inside a bolt compromises its specification and integrity.
All mechanical spring-loaded bolthead indicators (e.g., Smartbolt and Maxbolt), which change colour or move an indicator proportional to the applied tension, are useful for the initial installation, not monitoring the operation life.
There are wired or wireless load cell or strain-gauge-based disks used as washers, but they come with a minimum of 6 mm of thickness which makes them unsuitable in many applications. Also, Strain gauges consume electrical power that makes it impossible to be operated on a small battery.
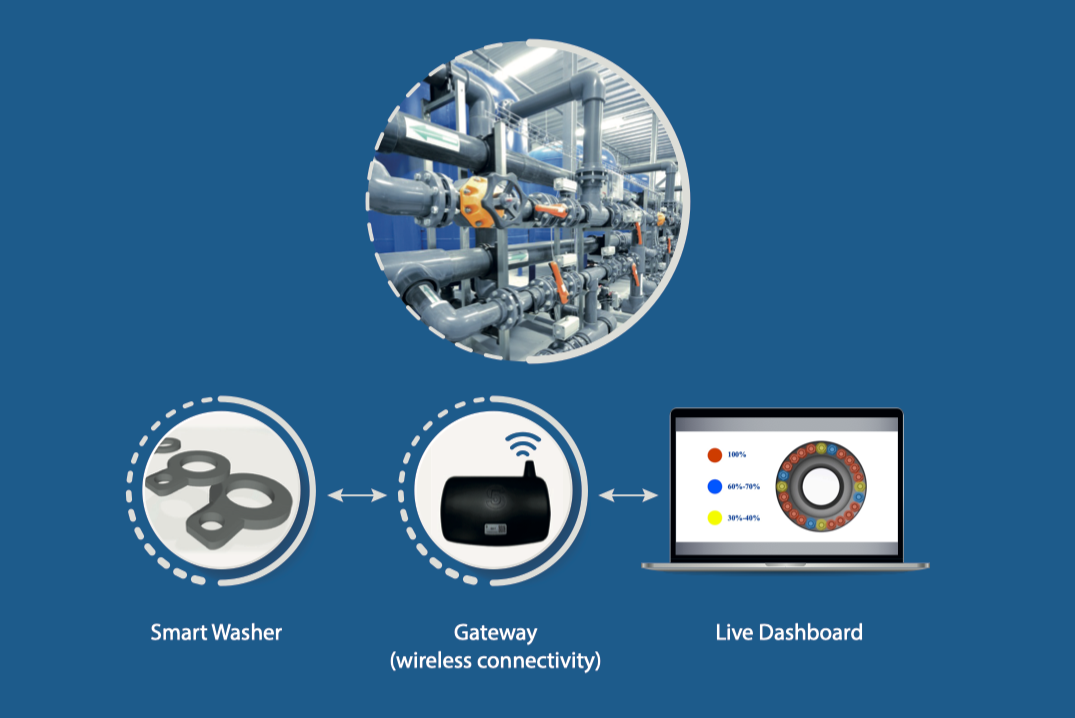
The Features:
- Minor cost of ownership with ROI in a few days.
- Minimal external footprint and no impact on the replacement /installation work.
- Manufactured in all standard sizes M10 to M63.
- Manufactured in major corrosion-resistant materials.
- Zero wiring requirements all washers are self-contained with the power from the battery, which lasts for five years and sends data wirelessly through their own network.
- With a graphical user interface and audio-visual alarm and remote operation/ maintenance notification.
- Completely waterproof and shockproof.
- With all self-diagnostic capabilities and zero calibration, this system guarantees no false or missed, or lost data feed.
- Access to the graphical user interface through mobile phones, tablets, laptops, and computers.
- Operating temperature ranges from -30 degrees to +120 degrees Celsius.
Benefits:
- Reduction or elimination of lost bolted joint integrity.
- Improved awareness and management of structural integrity.
- Ensures safety and integrity of bolted joints.
- Using the operational data and reports, the maintenance and reliability teams can better understand and manage their maintenance regimes plan usage and consumption of the material.
- Enables maintenance teams to be notified with an early warning when bolts become loose or approaching the end of life.